In today's competitive market, a great product alone isn't enough. Packaging plays a crucial role in protecting your product, attracting consumers, and conveying your brand's message. Yet many companies overlook the importance of thorough packaging testing, leading to damaged goods, confused customers, and lost sales.
Poor packaging can doom even exceptional products. Damaged items result in returns and negative reviews, and unclear labeling and unattractive designs fail to capture attention on crowded shelves. Moreover, non-compliant packaging risks costly recalls and legal issues, potentially devastating a business.
Comprehensive packaging testing offers a solution to these challenges. By evaluating your packaging's durability, functionality, and appeal, you ensure your product reaches consumers in perfect condition, stands out from competitors, and delivers an excellent user experience. This guide will explore how packaging testing can become your secret weapon for product success, helping you make informed decisions and gain a competitive edge in your market. Let's dive in.
Access Consumer Insights at Scale
What is Packaging Testing?
Packaging testing is a systematic process of evaluating and analyzing product packaging to ensure its quality, durability, functionality, and appeal. It involves subjecting packaging materials and designs to various tests that simulate real-world conditions, consumer interactions, and potential challenges throughout the supply chain.
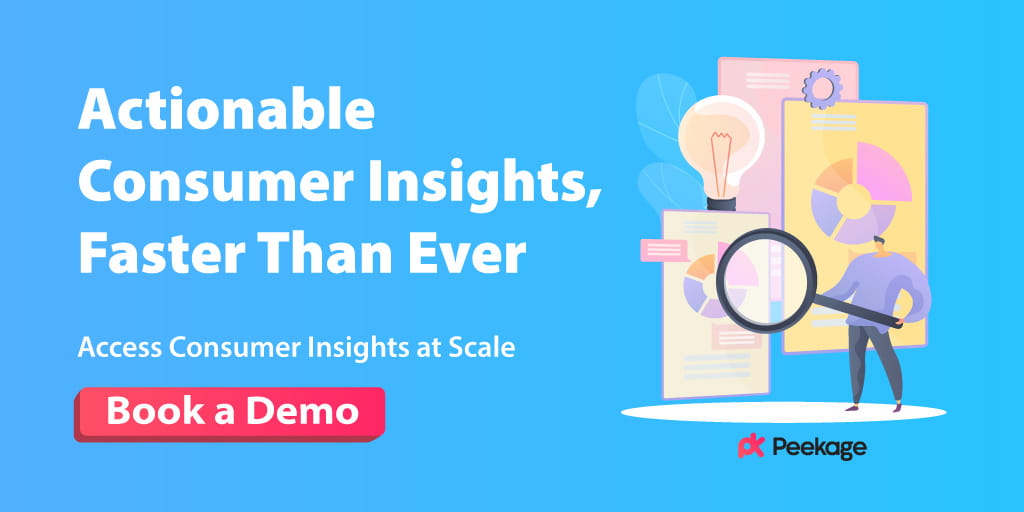
The Importance of Packaging Testing
Packaging testing is a crucial process that ensures the safety, integrity, and effectiveness of product packaging. The global packaging testing market is projected to reach USD 53,748.03 million by 2033, growing at a compound annual growth rate (CAGR) of 12.6% from 2023 to 2033.
Packaging testing offers numerous benefits for businesses, consumers, and the environment:
- Product Protection:
Rigorous testing ensures that packaging effectively shields products from damage during transportation, handling, and storage. This minimizes losses due to breakage or spoilage, reducing costs and improving customer satisfaction.
- Consumer Safety:
Testing verifies that packaging is safe for consumers to handle and use, preventing contamination and maintaining product integrity. This is particularly critical for food, pharmaceutical, and personal care items.
- Regulatory Compliance:
Packaging tests help ensure products meet industry standards and legal requirements. This reduces the risk of costly recalls, fines, or legal issues related to non-compliant packaging.
- Brand Image:
Well-designed and thoroughly tested packaging enhances consumer perception and trust. Products that arrive in pristine condition reinforce brand reputation and can provide a competitive advantage in the market.
- Cost Optimization:
Testing helps identify opportunities to reduce packaging costs without compromising quality. This may include material optimization, waste reduction, or more efficient designs.
- Environmental Impact:
As sustainability becomes increasingly important, packaging testing can assess the eco-friendliness of materials and support the development of more environmentally responsible solutions.
- Time-to-Market:
Comprehensive testing early in the development process helps avoid costly redesigns and delays, potentially accelerating product launches.
- Quality Assurance:
Regular testing ensures consistent packaging performance across production batches, maintaining high standards and reducing variability.
- Innovation Support:
Testing provides valuable data that can drive packaging innovations, leading to improved designs, materials, or functionalities.
- Supply Chain Efficiency:
Well-tested packaging can streamline logistics operations, reducing the need for excessive protective measures during shipping and handling.
By implementing a thorough packaging testing program, businesses can protect their products, satisfy customers, comply with regulations, optimize costs, and demonstrate their commitment to quality and sustainability. This holistic approach not only safeguards immediate business interests but also contributes to long-term brand success and environmental stewardship.
Types of Packaging Testing
Packaging testing is crucial for ensuring product safety and integrity throughout the supply chain. It encompasses a wide range of types, each used for evaluating specific aspects of packaging performance. These tests simulate various conditions and scenarios that packages may encounter throughout their lifecycle.
Here are the main categories of packaging tests, along with examples and their significance:
1. Physical Tests
These tests evaluate the structural integrity and durability of packaging.
- Drop testing: Assesses impact resistance during handling and transportation.
- Vibration testing: Simulates the effects of prolonged transportation.
- Compression testing: Evaluates stacking strength in warehouses or during shipping.
- Shock testing: Measures resistance to sudden impacts or changes in acceleration.
- Puncture resistance: Determines the package's ability to withstand sharp objects.
2. Environmental Tests
These tests simulate various environmental conditions packages may face.
- Temperature cycling: Assesses performance in fluctuating temperatures.
- Humidity testing: Evaluates moisture resistance and barrier properties.
- Altitude simulation: Tests package integrity at different atmospheric pressures.
- UV exposure testing: Measures resistance to sunlight and artificial light.
- Freeze-thaw cycling: Examines performance in cold chain logistics.
3. Chemical Tests
These tests focus on the interaction between the package and its contents or environment.
- Material compatibility testing: Ensures no adverse reactions between product and packaging.
- Permeation testing: Measures the transmission rate of gases or vapors through packaging.
- Leachable and extractable testing: Identifies potential contaminants from packaging materials.
- Corrosion testing: Assesses packaging's resistance to chemical degradation.
- Odor and taint testing: Evaluates the transfer of unwanted flavors or smells.
4. Functional Tests
These tests evaluate how well the packaging performs its intended functions.
- Seal integrity testing: Checks for leaks in sealed packages.
- Closure performance testing: Assesses the effectiveness of caps, lids, and other closures.
- Dispensing accuracy testing: Measures the precision of dosing or pouring mechanisms.
- Barrier property testing: Evaluates protection against oxygen, moisture, or light.
- Shelf life testing: Determines how long the packaging can maintain product quality.
5. Consumer-Oriented Tests
These tests focus on the end-user experience and packaging usability.
- Ease of opening: Evaluates accessibility, including for elderly or disabled users.
- Readability of instructions: Assesses clarity and legibility of packaging information.
- Child-resistance testing: Ensures compliance with safety standards for certain products.
- Reclosability testing: Checks the effectiveness of resealable features.
- Ergonomic testing: Evaluates handling comfort and ease of use.
6. Sustainability Tests
These tests assess the environmental impact of packaging.
- Recyclability testing: Determines how easily the packaging can be recycled.
- Biodegradability testing: Measures the rate of decomposition in various environments.
- Compostability testing: Assesses whether the packaging breaks down safely in composting facilities.
- Life cycle assessment: Evaluates the overall environmental impact from production to disposal.
7. Regulatory Compliance Tests
These tests ensure packaging meets legal and industry standards.
- Food contact material testing: Ensures safety for food packaging.
- Pharmaceutical packaging tests: Verifies compliance with drug packaging regulations.
- Hazardous materials packaging tests: Evaluates containment of dangerous goods.
- Medical device packaging tests: Ensures sterility and integrity for medical products.
Packaging Testing Methods
Building on our understanding of the importance and types of packaging testing, it's crucial to explore the various packaging testing methodologies used to conduct these evaluations. These methods bring to life the testing categories we discussed earlier, providing practical approaches to assess packaging performance, durability, and user experience.
Each method serves a specific purpose in the comprehensive evaluation of packaging, from controlled laboratory experiments to real-world consumer interactions. Let's examine the primary methods used in packaging testing:
Testing Method | Description | Benefits |
Laboratory Testing | Controlled environment testing using specialized equipment | - Precise, repeatable results - Quantitative data - Ability to isolate variables - Compliance with standardized protocols |
In-Transit Testing | Real-world testing during actual shipping and handling | - Identifies issues in the supply chain - Reflects actual conditions - Reveals unforeseen challenges - Validates laboratory results |
Simulated Use Testing | Mimics consumer interaction with the packaging | - Evaluates user experience and functionality - Identifies potential usability issues - Assesses ergonomics and convenience |
Accelerated Aging Tests | Exposes packaging to extreme conditions to predict long-term performance | - Faster results - Identifies potential issues early - Estimates shelf life - Evaluates material degradation |
Consumer Feedback Testing | Gathers opinions and experiences from target consumers | - Direct insights into user preferences - Identifies pain points - Assesses market acceptance - Informs design improvements |
Virtual Testing | Uses computer simulations and digital models to analyze packaging performance | - Cost-effective for initial designs - Allows rapid iteration - Reduces physical prototyping needs - Evaluates complex scenarios |
Non-Destructive Testing | Examines packaging integrity without damaging the product or package | - Allows for 100% inspection- Ideal for high -value or sensitive products - Detects internal defects - Supports quality control |
Each of these methods plays a crucial role in comprehensive packaging testing. Let's review them:
a) Laboratory Testing:
Forms the backbone of most testing programs, providing controlled, repeatable results that can be easily quantified and compared against standards.
b) In-Transit Testing:
Bridges the gap between lab results and real-world performance, uncovering issues that may not be apparent in controlled environments.
c) Simulated Use Testing:
Focuses on the end-user experience, ensuring that packaging not only protects the product but also enhances consumer interaction.
d) Accelerated Aging Tests:
Are vital for predicting long-term performance, especially for products with extended shelf lives or those exposed to harsh environments.
e) Consumer Feedback Testing:
Provides invaluable insights into market acceptance and user preferences. Innovative approaches like Peekage, which allows brands to conduct targeted product sampling and research campaigns with consumers in their homes, offer a deeper understanding of packaging performance in real-world settings.
f) Virtual Testing:
Has become increasingly important in the early stages of packaging design, allowing for rapid iteration and optimization before physical prototypes are created. This method utilizes advanced computer-aided design (CAD) software and finite element analysis (FEA) tools to simulate various conditions and stresses on packaging designs.
Virtual testing is particularly valuable for complex or expensive packaging designs, as it can significantly reduce the time and cost associated with physical prototyping. However, while highly informative, virtual testing results should typically be validated with physical tests before final implementation.
g) Non-Destructive Testing:
Methods, such as X-ray inspection or ultrasonic testing, are particularly valuable for high-value products or in industries with stringent quality control requirements.
The most effective packaging testing strategies often combine multiple methods to provide a comprehensive evaluation. For example, a new food packaging design might undergo laboratory testing for barrier properties, accelerated aging to determine shelf life, simulated use testing to assess consumer interaction, and finally, consumer feedback testing to gauge market acceptance.
By employing a multi-faceted approach to packaging testing, companies can ensure their packaging not only meets regulatory requirements and protects the product but also resonates with consumers and performs well throughout the supply chain.
Packaging Testing Process
The packaging testing process is a systematic approach to evaluating and validating packaging designs. This process ensures that packaging meets all requirements for product protection, consumer safety, and regulatory compliance. Here's a detailed breakdown of the key steps involved:
Step One: Define Objectives and Requirements
- Identify specific testing goals based on product characteristics, target market, and intended use
- Review applicable industry standards and regulatory requirements
- Consider environmental factors, shipping methods, and storage conditions
Step Two: Develop a Testing Strategy
- Create a comprehensive testing plan that addresses all identified objectives
- Prioritize tests based on critical-to-quality attributes and risk assessment
- Determine sample sizes and testing frequencies
Step Three: Select Appropriate Tests
- Choose relevant tests from categories such as physical, chemical, environmental, and functional
- Consider both standard industry tests and custom tests specific to your product
- Ensure selected tests simulate real-world conditions as closely as possible
Step Four: Prepare Test Samples
- Gather representative samples of the packaging materials and finished packages
- Ensure samples accurately reflect production materials and processes
- Document sample preparation methods and any pre-conditioning required
Step Five: Conduct Testing
- Perform tests in controlled environments using calibrated equipment
- Follow standardized testing protocols to ensure consistency and repeatability
- Document all test procedures, conditions, and observations in detail
Step Six: Analyze and Interpret Results
- Compile and organize test data for thorough analysis
- Compare results against predefined acceptance criteria and industry standards
- Identify any failures, weaknesses, or areas for improvement
- Consider statistical analysis for quantitative tests to ensure the reliability of results
Step Seven: Generate a Comprehensive Report
- Summarize test methods, results, and conclusions in a clear, concise manner
- Include visual aids such as graphs or images to illustrate key findings
- Highlight any non-conformances or areas requiring further investigation
Step Eight: Implement Improvements
- Develop action plans to address any identified issues or opportunities for enhancement
- Collaborate with design and production teams to implement necessary changes
- Consider cost-benefit analysis for proposed modifications
Step Nine: Verify and Validate
- Retest modified packaging to confirm the effectiveness of improvements
- Conduct limited field trials or pilot runs if significant changes were made
- Update packaging specifications and quality control procedures as needed
Step Ten: Continuous Monitoring and Improvement
- Establish ongoing testing protocols for production quality control
- Regularly review and update testing processes to align with new technologies or regulations
- Gather and analyze customer feedback and field performance data
Step Eleven: Documentation and Record Keeping
- Maintain detailed records of all testing activities, results, and subsequent actions
- Ensure traceability of testing samples and data for future reference or audits
- Use data to inform future packaging development projects
This comprehensive process ensures companies that their packaging designs are thoroughly evaluated, optimized, and validated before full-scale production and market launch. This systematic approach not only minimizes the risk of packaging failures but also contributes to continuous improvement in packaging performance and efficiency.
Remember that the packaging testing process should be flexible and iterative. Depending on the complexity of the packaging and the nature of the product, some steps may need to be repeated or expanded. Additionally, involving cross-functional teams throughout the process can provide valuable insights and ensure all aspects of packaging performance are considered.
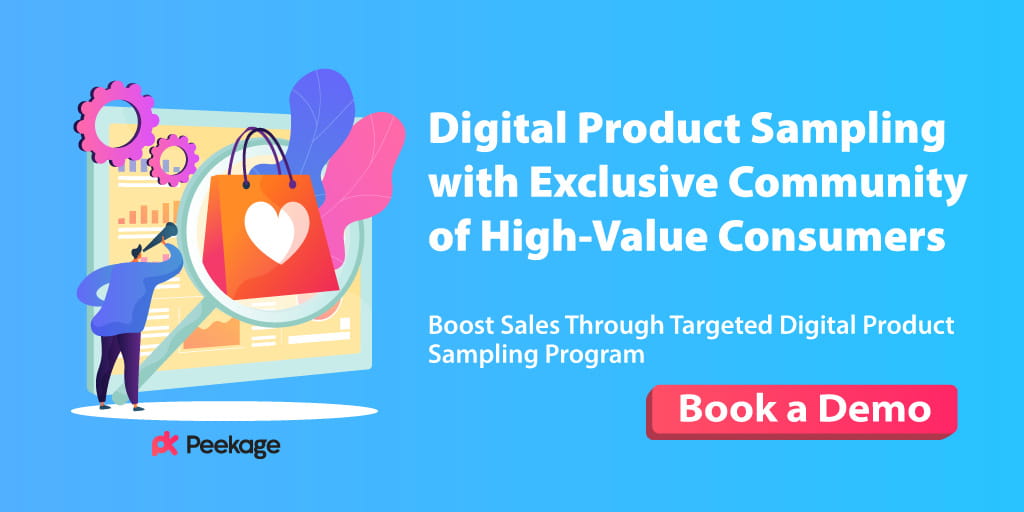
Key Factors to Consider in Packaging Testing
Effective packaging testing requires a holistic approach that takes into account various factors affecting the packaging's performance, safety, and market success. When designing and implementing a packaging testing program, consider the following key factors:
- Product Characteristics
- Physical properties (e.g., fragility, weight, dimensions)
- Chemical composition and reactivity
- Shelf life and stability requirements
- Sensitivity to environmental factors (temperature, humidity, light)
- Special handling needs (e.g., sterility for medical products)
- Target Market and Consumer Behavior
- Demographics and preferences of target consumers
- Cultural considerations in different markets
- Consumer usage patterns and expectations
- Accessibility needs (e.g., ease of opening for elderly or disabled users)
- Potential misuse scenarios
- Distribution Channel and Supply Chain
- Transportation methods and durations
- Storage conditions throughout the supply chain
- Handling processes (e.g., automated vs. manual)
- Potential stacking and compression scenarios
- Exposure to varying climatic conditions during transit
- Regulatory Requirements and Industry Standards
- Compliance with local, national, and international regulations
- Industry-specific standards (e.g., food safety, pharmaceuticals)
- Labeling and information requirements
- Child-resistant packaging regulations where applicable
- Export market regulations if selling internationally
- Sustainability and Environmental Impact
- Recyclability and biodegradability of materials
- Carbon footprint of packaging production and transportation
- Compliance with eco-labeling schemes
- Potential for packaging reuse or upcycling
- Alignment with circular economy principles
- Cost Considerations and Economic Factors
- Balance between testing thoroughness and budget constraints
- Cost-benefit analysis of different testing methods
- Potential cost savings from optimized packaging design
- Long-term economic impact of packaging failures vs. testing investment
- Scalability of testing for different production volumes
- Brand Image and Marketing Strategy
- Alignment of packaging design with brand values and positioning
- Unboxing experience and its impact on brand perception
- Competitive differentiation through packaging innovation
- Packaging's role in product storytelling and communication
- Consistency across product lines and packaging families
- Manufacturing and Production Processes
- Compatibility with existing production equipment
- Consistency and quality control in packaging production
- Scalability of packaging solutions for different batch sizes
- Impact of packaging on production line efficiency
- Technological Advancements
- Integration of smart packaging features (e.g., QR codes, NFC tags)
- Compatibility with e-commerce and last-mile delivery systems
- Potential for incorporating anti-counterfeiting measures
- Adaptation to emerging packaging materials and technologies
- Risk Assessment and Mitigation
- Identification of critical failure points in packaging
- Evaluation of worst-case scenarios and stress conditions
- Consideration of product-package interaction over time
- Assessment of tampering risks and security features
- User Experience and Functionality
- Ease of opening, reclosing, and dispensing
- Clarity of instructions and product information
- Ergonomics and handling comfort
- Storage convenience for consumers
- Lifecycle Analysis
- Environmental impact from raw material extraction to disposal
- Energy consumption in packaging production and transportation
- End-of-life considerations (recyclability, biodegradability)
- Potential for packaging lightweight or material reduction
Considering these factors can help companies develop a comprehensive packaging testing strategy that addresses all aspects of packaging performance, from protection and preservation to user experience and environmental impact. This holistic approach ensures that packaging not only meets technical and regulatory requirements but also aligns with broader business goals, consumer expectations, and sustainability objectives.
Tools and Techniques for Effective Packaging Testing
Effective packaging testing combines cutting-edge technology with time-tested methodologies to ensure packaging meets all necessary performance criteria. This section explores the essential tools and techniques used in modern packaging testing laboratories.
- Advanced Laboratory Equipment
At the heart of any packaging testing facility is its array of specialized equipment. Tensile testers and compression machines evaluate material strength, while environmental chambers simulate various temperature and humidity conditions.
Impact resistance is assessed using drop test machines, and vibration tables replicate transportation stresses. For more specific tests, burst testers evaluate package integrity, and gas chromatographs analyze permeation and migration.
- Software Solutions for Analysis and Simulation
The digital revolution has transformed packaging testing. Computer-Aided Design (CAD) software and Finite Element Analysis (FEA) tools allow for virtual prototyping and stress simulation, significantly reducing development time and costs.
Statistical analysis software helps interpret complex data sets, while Laboratory Information Management Systems (LIMS) streamline data organization and reporting.
- Non-Destructive Testing Innovations
Recent advancements in non-destructive testing have opened new possibilities in packaging evaluation. X-ray inspection and ultrasonic testing allow for the internal examination of packages without compromising their integrity. Thermal imaging can assess heat sealing quality, while acoustic emission testing detects micro-cracks invisible to the naked eye.
- Real-Time Monitoring and Data Collection
The Internet of Things (IoT) has enabled real-time monitoring of packages during transit. RFID tags and smart sensors can now collect data on shock, vibration, and environmental conditions throughout the supply chain, providing valuable consumer insights into real-world package performance.
- Accelerated Aging and Environmental Simulation
To predict long-term performance, accelerated aging equipment like weatherometers and xenon arc chambers simulate extended environmental exposure in a compressed timeframe. This allows testers to evaluate how packaging materials will degrade over months or years of use.
- Consumer-Centric Testing Approaches
Understanding the end-user experience is vital. Eye-tracking devices and in-home usage tests (IHUTs) provide valuable data on how consumers interact with packaging. Online survey platforms facilitate quick feedback collection, informing both functional and aesthetic aspects of packaging design.
- Sustainability Assessment
Studies show that 74% of consumers are willing to pay more for sustainable packaging. As environmental concerns continue to rise, tools for assessing packaging sustainability have become essential. Life Cycle Assessment (LCA) software helps evaluate the environmental impact of packaging from production to disposal. Specialized equipment for testing biodegradability and recyclability ensures compliance with eco-friendly initiatives.
- Adherence to Industry Standards
Standardization is crucial in packaging testing. Laboratories typically follow protocols set by organizations such as ASTM International, the International Safe Transit Association (ISTA), and the International Organization for Standardization (ISO). These standards ensure consistency and comparability of test results across different facilities and countries.
Integrating Tools and Techniques
The key to effective packaging testing lies not just in having advanced tools, but in integrating them into a cohesive testing strategy. This involves:
- Regularly calibrate and maintain all testing equipment to ensure accuracy.
- Train personnel in the proper use of tools and interpretation of results.
- Stay updated on the latest industry standards and testing methodologies.
- Implement a robust data management system to track and analyze test results over time.
- Collaborate with cross-functional teams to align testing protocols with product development and marketing strategies.
- Consider partnering with specialized testing laboratories for access to advanced equipment and expertise.
By leveraging these tools and techniques, companies can conduct comprehensive packaging tests that evaluate all aspects of performance, from structural integrity to consumer appeal. This multifaceted approach helps ensure that packaging not only meets regulatory requirements but also delivers optimal protection, functionality, and user experience throughout the product lifecycle.
Challenges in Packaging Testing
While packaging testing is essential, it comes with its own set of challenges:
- Time Constraints: Thorough testing can be time-consuming, potentially delaying product launches.
- Cost Considerations: Comprehensive testing programs can be expensive, especially for smaller brands.
- Balancing Requirements: Finding the right balance between protection, aesthetics, and sustainability can be challenging.
- Keeping Up with Innovations: As packaging materials and technologies evolve, testing methods must adapt accordingly.
- Simulating Real-World Conditions: Accurately replicating the diverse conditions a package may encounter can be difficult.
- Interpreting Results: Translating test data into actionable insights requires expertise and careful analysis.
Best Practices for Effective Packaging Testing
To maximize the benefits of packaging testing and overcoming challenges, consider these best practices:
- Start Early: Integrate testing into the early stages of packaging design to avoid costly changes later.
- Develop a Comprehensive Plan: Create a testing strategy that covers all relevant aspects of packaging performance.
- Use a Combination of Methods: Employ both laboratory and real-world testing for a holistic evaluation.
- Involve Stakeholders: Collaborate with suppliers, logistics partners, and retailers to address concerns throughout the supply chain.
- Stay Informed: Keep up-to-date with the latest testing standards and technologies in the packaging industry.
- Document Everything: Maintain detailed records of test procedures, results, and actions taken.
- Continuously Improve: Use insights from testing to refine and optimize packaging designs over time.
- Consider Outsourcing: Partner with specialized testing facilities or use platforms for consumer testing to access expertise and resources.
The Future of Packaging Testing
As technology advances and consumer expectations evolve, packaging testing is likely to see several exciting developments:
- AI and Machine Learning: Predictive modeling to optimize packaging designs and testing protocols.
- Virtual and Augmented Reality: Simulating consumer interactions with packaging in virtual environments.
- IoT-Enabled Testing: Smart sensors to monitor package conditions throughout the supply chain in real-time.
- Sustainability Metrics: More sophisticated tools for assessing the environmental impact of packaging materials.
- Personalization Testing: Evaluating the performance of customized packaging solutions.
- Nanotechnology: Testing the effectiveness of advanced materials with unique protective properties.
- Blockchain Integration: Ensuring the authenticity and traceability of packaging materials and test results.
Conclusion
Packaging testing is a critical process that ensures the success of your products in the market. By thoroughly evaluating packaging performance, brands can protect their products, enhance customer satisfaction, and gain a competitive edge. As the packaging industry continues to evolve, staying informed about the latest testing methods and technologies will be crucial for success.
Remember, effective packaging testing is not just about meeting standards; it's about creating packaging that resonates with consumers, protects your product, and aligns with your brand values. By investing in comprehensive packaging testing, you're investing in the long-term success of your product and brand.
FAQs
1. How do you test packaging?
To test packaging, conduct a visual inspection for defects and alignment, perform functional tests to ensure proper opening and closing, and carry out durability tests by simulating handling, shipping, and storage conditions. Additionally, analyze materials to verify they meet required specifications, check for compliance with regulatory and industry standards, and gather feedback from consumers on ease of use and satisfaction.
2. What is ASTM in packaging?
ASTM in packaging refers to standards set by ASTM International that specify testing methods and requirements to ensure packaging materials and products meet quality, safety, and performance criteria.
3. How do you measure quality of packaging?
The quality of packaging is measured by assessing its durability, functionality, compliance with standards, visual appeal, material quality, and consumer feedback. Testing involves durability simulations, material analysis, and user satisfaction surveys.
4. What are ISO standards for packaging?
ISO standards for packaging are internationally recognized guidelines set by the International Organization for Standardization (ISO) that define requirements and testing methods to ensure packaging quality, safety, efficiency, and environmental impact.
References
- 4 Best Practices For Consumer-Centric Packaging, Premium Packaging,
https://premiumpackaging.com.au/blog/4-best-practices-for-consumer-centric-packaging/ - Packaging Testing Market Outlook, Future Market Insight,
https://www.futuremarketinsights.com/reports/packaging-testing-market - Guide to Protective Packaging Materials for Shipping, Grainger,
https://www.grainger.com/know-how/equipment/kh-shipping-guide-types-protective-packaging - Methods Available for Testing Packaging Strength, Pack Size,
https://www.packsize.com/blog/methods-available-for-testing-packaging-strength - Testing laboratory packaging tests / sterile barrier systems, SteriXpert,
https://www.sterixpert.de/en/testing-laboratory-packaging-tests.html